The Heavy Goal of “LightWeighting”
The lighter a vehicle is, the lesser energy it consumes thus improving fuel economy and greenhouse gas emissions. Light-weighting is a goal in tune with the increasingly stringent global environmental legislations. Automotive companies are constantly on a look out for light-weighting while keeping cost considerations in place.
Aluminium is known for its versatility, strength, flexibility, malleability, conductivity, reflectivity and corrosion resistance. In specific performance metrics like mechanical strength and stiffness, it is better suited among new-age metals in designing vehicle components. Aluminium has been a metal of choice for almost two decades for doors of premium segment cars and now in the SUV segment, Pick-up trucks and EVs – that are being made from aluminium and alloy combinations.
The automobile industry is investing heavily and advancing rapidly to achieve the best results in fuel economy, controlling emissions and C.A.S.E.
Light-weighting is the answer to many of these worthy goals for e.g., a 10% reduction in weight may result in 7% reduction in fuel consumption.
Advancements in Aluminium
Recent advancements in material utilisation, processing and joining are allowing Aluminium Doors to be more cost-effective than ever before. Due to innovative joining techniques, fewer parts are required in the vehicle, further reducing complexity and assembly time. Alumobility, a global ecosystem of leading aluminium and downstream technology partners, studies these aspects and has also worked on the B-pillar, which is one of the most complex parts of the vehicle structure. Due to its importance in both integrity and safety, B-pillar has traditionally been very heavy. Light-weighting without compromising on core requirements was the goal. Alumobility tested a popular mass-production vehicle by using high-strength 6XXX aluminium alloys and achieved 31% light-weighting. The current alloy combinations are also compatible with other aluminium alloys used on production vehicles that simplify end-of-life recycling. According to Alumobility, the next generation aluminium door design can offer greater value due to lower gauges and higher strength levels through new innovative aluminium alloys that are now becoming available.
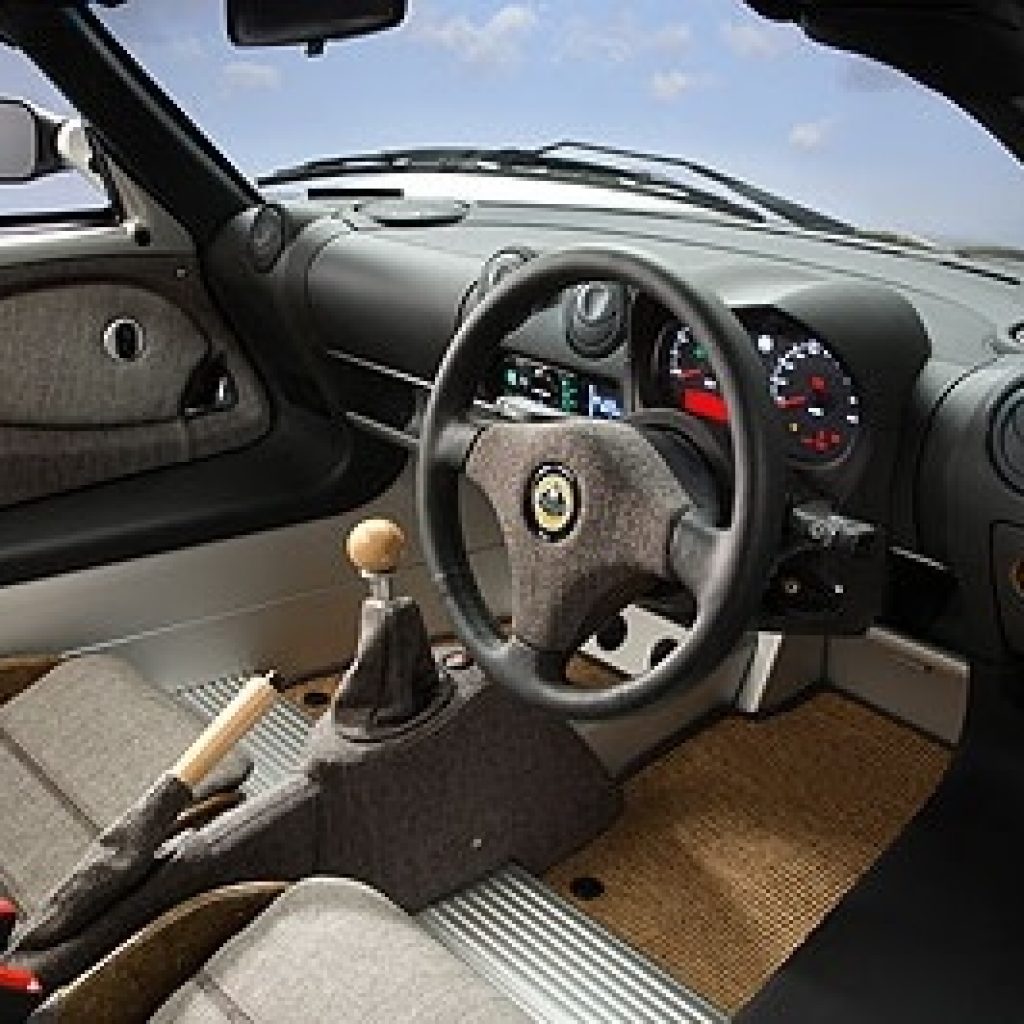
Industry Approach to Light-weighting
The automotive industry considers 3 main focus areas to achieve light-weighting viz. Materials & Components; Lower Power Engines; Aerodynamic Body Designing
I. Materials such as iron and steel are being replaced by aluminium and composites in car parts. Examples include – BMW’s Carbon Core technology in its Series 7 chassis through its CLAR platform ; Volkswagen that managed to eliminate 100 kg from its new Golf model using technologies such as sheet metal, hot-formed components and high to ultra-strength metals – cheaper than aluminium and carbon fibre ; Ford that uses aluminium to replace steel and carbon fibre for various interior components in its F-150 achieving a 800 pounds weight reduction ; Mazda that has been working on replacing lead-acid batteries with the much lighter lithium-ion units, etc. Another metal – Magnesium is 33% lighter than aluminium and is already being used in sports cars. Upholstery and dashboards are being replaced by unusual materials like banana leaves, hemp, kenaf and soy as well as advanced plastics.
The advancements in polymers and improvements in plastic stabilizers and dyes have made plastics beneficial to the industry in several ways. BASF’s solutions include:
1.Chem-Cycling initiative – use of pyrolysis oil from plastic waste
2.Kaolin’s Translink® – performance mineral extenders
3. Elastoflex® – injected into the vehicles body to fill cavities and sills
4. Acrodur – thermoset water-based technology, resin-reinforced, formaldehyde-free, cross-linking resin
II. Engine light-weighting has seen Ford adopt the 1.0 Ecoboost turbo three-cylinder engine for its Fusion Light-weight concept. This engine gives a fuel economy of 45mpg equivalent to a Ford Fiesta while the lower weight guarantees a vehicle that runs at the performance of a Ford Fusion, with a 2.5 litre engine.
III. Aerodynamic characteristics play an important role in design and manufacture of vehicles, especially for cars. In order to produce high-performance, fuel-efficient, and environmentally friendly models, it is necessary to optimize the design of the vehicle to ensure both aesthetics and desired aerodynamic characteristics. A light weight car with an efficient engine that also incorporates Aerodynamic design requires even lesser fuel.
As innovative solutions for light-weighting continue, the major factors to be considered are Cost and Accessibility of exotic or newer raw materials.
Newton demonstrated: Force = Mass * Acceleration
All efficient solutions benefit from moving less weight. Powertrain efficiency improves when it uses a reduced force to accelerate a reduced mass. Reduction of mass in EVs enables the use of a smaller battery by reducing the energy consumption thus directly contributing to reduction in the cost of the battery as well.
Cost and Raw Material Availability Considerations
One of the biggest attractions of light-weighting vehicles is achieving secondary weight savings better known as mass decompounding effects. This means that mass reduction in one area leads to further weight reduction possibilities in other areas. It is seen that closures offer potentially more weight savings than other areas of the vehicle as reducing 20 kg in closure mass leads to approximately 20 kg reduction in the vehicle mass. The converse is not true and reducing weight from other areas does not allow for mass decompounding of closures.
Mass reduction positively enables fuel economy and reduces emissions as already discussed.
However, too often, the costs associated with mass reduction are oversimplified. Lightweight engineered solutions require a systems approach in place of a simple material substitution approach so as to arrive at accurate cost estimates of mass reduction. Integrated parts that combine to become one part is an area of growth in light-weight solutions. It not only helps reduce the weight but also the assembly cost by combining functionality and structural requirements.
Challenges faced in manufacturing of light-weight solutions are multifarious viz. disturbance of existing supply chains due to newer or exotic materials applications, new ways of design modelling leading to change in existing design standards and best practices, new tooling, new equipment, forming technologies, joining methods, assembly orientations, regularising production rates after the disruption caused due to new materials, etc. Hitherto, only high-end vehicles having sufficient margins were exposed to light-weighting possibilities. However, the increasing demand for clean and efficient vehicles has brought the concept to mass produced vehicles – and while smaller margins might not justify, higher volumes can help offset the investment in tooling and equipment due to newer technologies. Further, efficiencies through product engineering, mass decompounding effects, consolidation of parts, gradual testing of lower grade light-weighting materials, etc. can help mitigate high costs as well.
Conclusion
Automotive light-weighting is aimed at sustainability together with performance. It is a strategy that is part of the concept of circular economy that is not exclusively focused on weight reduction alone but also on structural efficiency while addressing environmental and economic concerns.
In addition to design, materials are a key contributor to light-weighting. New lightweight material typically has a cost premium increase from the conventional material. The need for materials that fit the bill has created challenges and opportunities for existing metallic alloys as well as mixed materials approach, metal-matrix composites, laminates, sandwich structures and bionic-inspired archetypes.
Manufacturing still remains a limitation however progress in additive manufacturing, integrated parts to reduce components and combined manufacturing processes that lead to reduced stations, reduced transfer equipment and a reduced number of tooling dies – are likely to eliminate hurdles.
For more information on how a foreign company can sell light-weighting solutions in the Indian market write to me at sudhir.nerurkar@quanzen.com